The production process of the famous wheel is much more involved than you might expect
13 hours ago
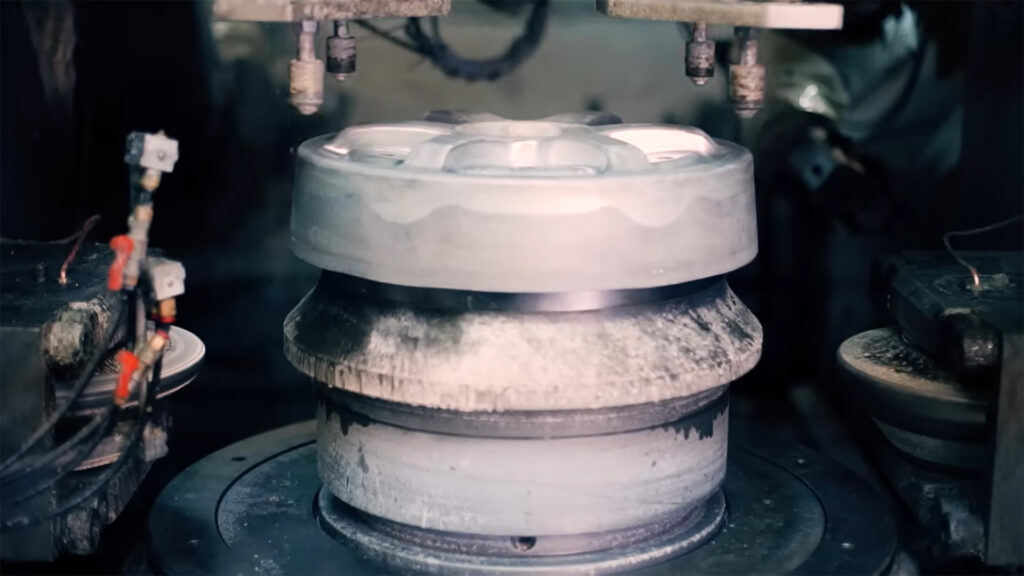
When talking about wheels, it’s impossible not to mention the iconic RAYS TE37. Their timeless design works with everything from Fords to Ferraris, earning them their lasting legendary status in the car community. Now, if you’ve ever wondered how they’re made, you’re in luck, because RAYS themselves put out a video going through their full manufacturing process from start to finish.
Each TE37 starts its life as a solid aluminum cylinder, also called a billet. These billets are made of a proprietary Aluminum 6061 alloy specially formulated by RAYS, one which places a heavy focus on strength. Each billet is then heated to allow it to be more workable for the forging to come.
Once heating is complete, the billet then moves on to the forging process. This 3-step process begins with a preliminary forging die that stamps the billet into a rough shape of the finished wheel. From there, a secondary forging die comes in and refines the shape of the spokes, hollowing them out in the process. The final step of forging sees these hollowed-out channels shaped into a U-profile to achieve the desired strength and rigidity, all while maintaining a light weight.
advertisement scroll to continue
See Also: Seat X-Rays Its Wheels To Make Sure They’re Absolutely Flawless
Related: Aussie-Based Carbon Revolution Creates the World’s First One-Piece Carbon Fiber Rim
Next, the wheel is heated again, and a forming rotor to is used to take the outer profiles of the cylinder from a flat profile to the complex flared shape we associate with automotive wheels. Following this, the wheel undergoes a heat-treating process of quenching and tempering to optimize the aluminum’s tensile strength, proof stress, and elongation.
Next up is mounting processing, which involves performing various CNC operations to achieve an even surface finish, balance the wheel, and add the mounting/valve stem holes. These may seem like simple operations, but the tight tolerances they require necessitate an extreme level of precision. Once this is done, the remaining burrs from the machining process are removed. Not only does this make the wheel look better, but it also allows for better adhesion of paint and corrosion-resistant coatings.
Once manufacturing is done, each wheel is subjected to a radial load fatigue test to determine how the wheels hold up over a multitude of rotations. Once it’s found to meet RAYS’ standards, it’s polished, shot-blasted, degreased, and powder-coated, then diamond-cut and painted for the final surface finishing. Lastly, automated engravers and painting machines add the necessary details to the finished product before a final human inspection and strength testing certify the wheels to be shipped out to customers.